Assam-Magnetic polishing machines and electrolytic polishing are two common surface treatment technologies that differ in many aspects. Firstly, let’s take a look at an overview of these two technologies.
Magnetic polishing machine is a device that uses magnetic grinding technology to polish metal surfaces. It generates relative motion between the grinding body and the metal surface through the action of magnetic field and grinding fluid, thereby achieving the purpose of polishing. Electrolytic polishing, on the other hand, is a method of polishing metal surfaces using electrochemical reactions. It produces an anodic dissolution reaction on the metal surface, gradually making it smooth.
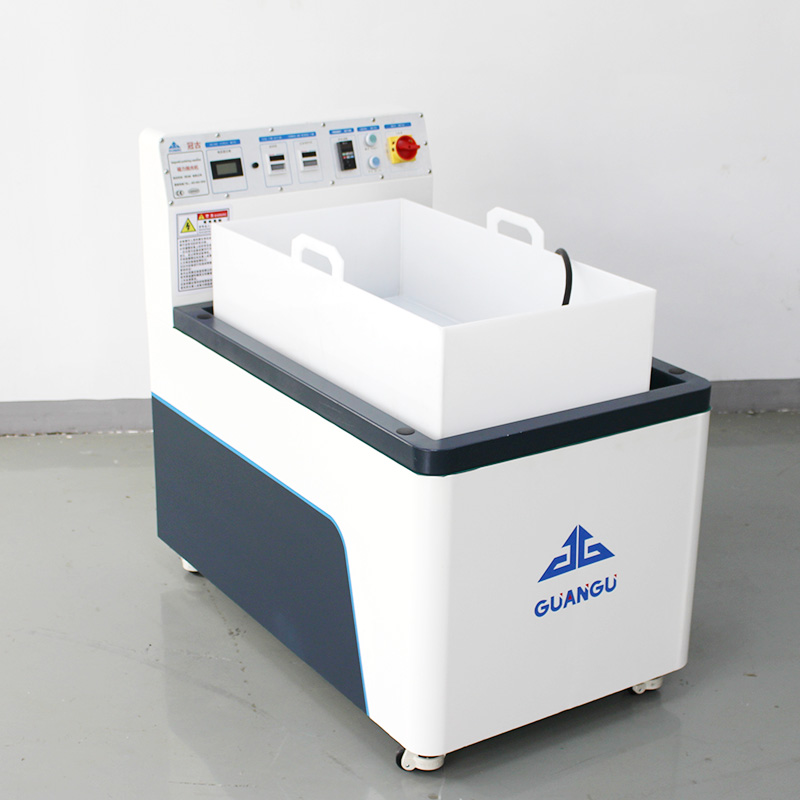
Next, we will conduct a detailed comparison between magnetic polishing machines and electrolytic polishing from the following aspects: Firstly, in magnetic polishing machines, the interaction between magnetic field and grinding fluid is crucial. The magnetic field causes the grinding body to suspend on the metal surface, while the grinding fluid plays a role in lubrication and grinding. When there is relative motion between the grinding body and the metal surface, the magnetic field force and the grinding fluid work together to achieve a polishing effect on the metal surface.
Electrolytic polishing, on the other hand, utilizes electrochemical reactions to anodic dissolve the metal surface. In the process of electrolytic polishing, the metal workpiece is connected to the positive pole of the power supply, and the anode is connected to the negative pole of the power supply. The chloride ions in the electrolyte discharge on the anode, producing chlorine gas and hydrogen gas. As chlorine and hydrogen gas continue to escape, the oxide film on the metal surface is gradually removed, and the metal surface gradually becomes smooth.
2、 The processing effect of magnetic polishing machine is mainly manifested in removing burrs, scratches, and oxide layers on the metal surface, while also improving the surface roughness. Due to the physical grinding method used by magnetic polishing machines, they do not have a significant thermal impact on the metal surface, making them suitable for polishing various metal materials.
The processing effect of electrolytic polishing is mainly manifested in improving the roughness and glossiness of the metal surface. By removing the oxide film and small protrusions on the metal surface, electrolytic polishing can make the metal surface smooth and have high reflectivity. In addition, electrolytic polishing can also form a passivation film on the metal surface, improving the corrosion resistance of the metal.
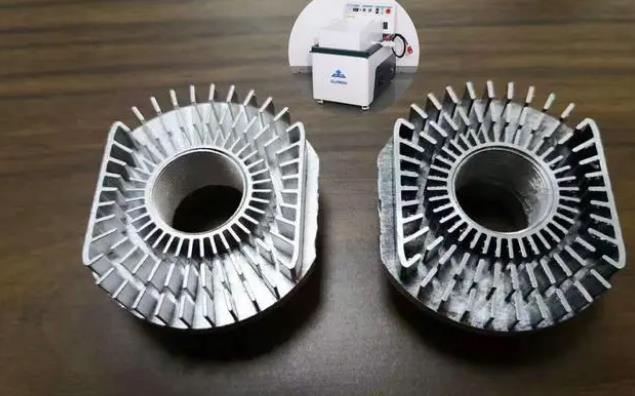
3、 Due to the use of physical grinding, magnetic polishing machines are suitable for polishing various metal materials, such as stainless steel, iron, copper, aluminum, etc. At the same time, magnetic polishing machines are also widely used in various fields such as mechanical parts, automotive parts, and medical devices.
Electrolytic polishing is mainly applied to the processing of metal materials with high conductivity such as copper and its alloys, stainless steel, etc. In fields such as electronics, communication, aerospace, and chemical industry, electrolytic polishing is often used to manufacture high-precision parts and components.
4、 The advantages and disadvantages of magnetic polishing machines are good processing efficiency, wide applicability, simple operation, and convenient maintenance. However, magnetic polishing machines also have certain limitations, such as low processing efficiency for some high-precision and complex shaped parts.
The advantage of electrolytic polishing is that it can improve the glossiness and corrosion resistance of metal surfaces, and is suitable for various metal materials with high conductivity. However, the cost of electrolytic polishing is relatively high, and for some non-conductive materials, it may not be possible to process them.
In short, magnetic polishing machine and electrolytic polishing are two different surface treatment technologies, which have certain differences in processing principles, processing effects, application scope, advantages and disadvantages. The specific method to be selected depends on actual needs and process requirements.